06.05.2024
Solving AGVs increase productivity by 30% in DMG MORI’s new Excellence Factory
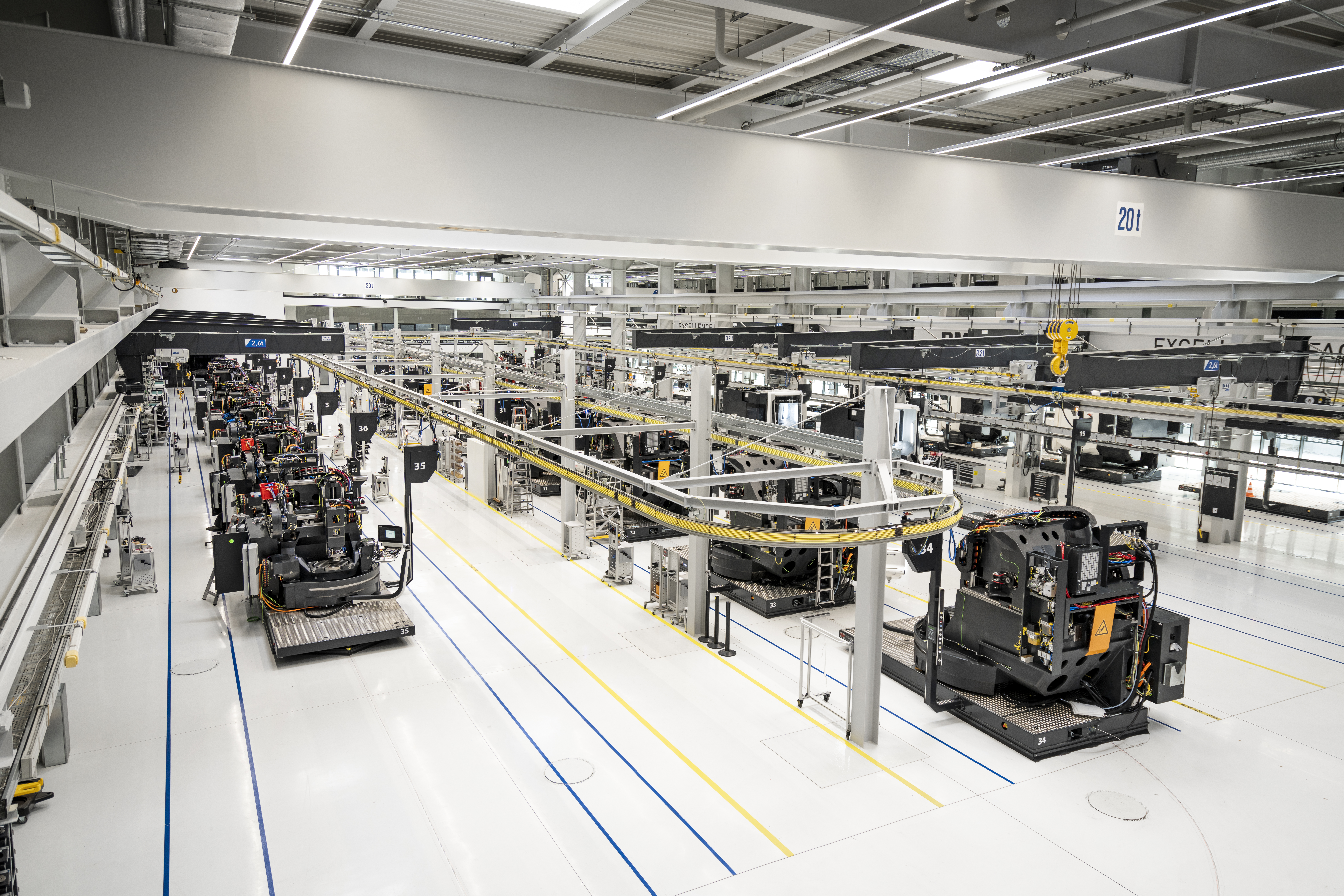
In 2019, Solving started collaborating with the German machine manufacturer DMG MORI Pfronten GmbH. The machine manufacturer has an annual production capacity of over 1,000 machines and employs 1,200 people on the 149,000m² company site. Eight machine types from the monoBLOCK series are assembled on automated mobile Solving platforms in the new Excellence Factory. The investment has increased overall productivity by 30%.
Objective
The machine manufacturer’s objective was to switch from their previous assembly line on rails to continuous flow assembly to be able to increase productivity by 30%. The automated guided vehicles, AGVs, should be installed to cover the entire production cycle. Assembly as well as all measurements and test runs should be carried out on the new assembly platforms.
After a selection process, Solving was chosen among 22 suppliers for the project with 36 AGVs. The decision was made due to Solving’s technical expertise and rapid feedback on technical issues, among other things.
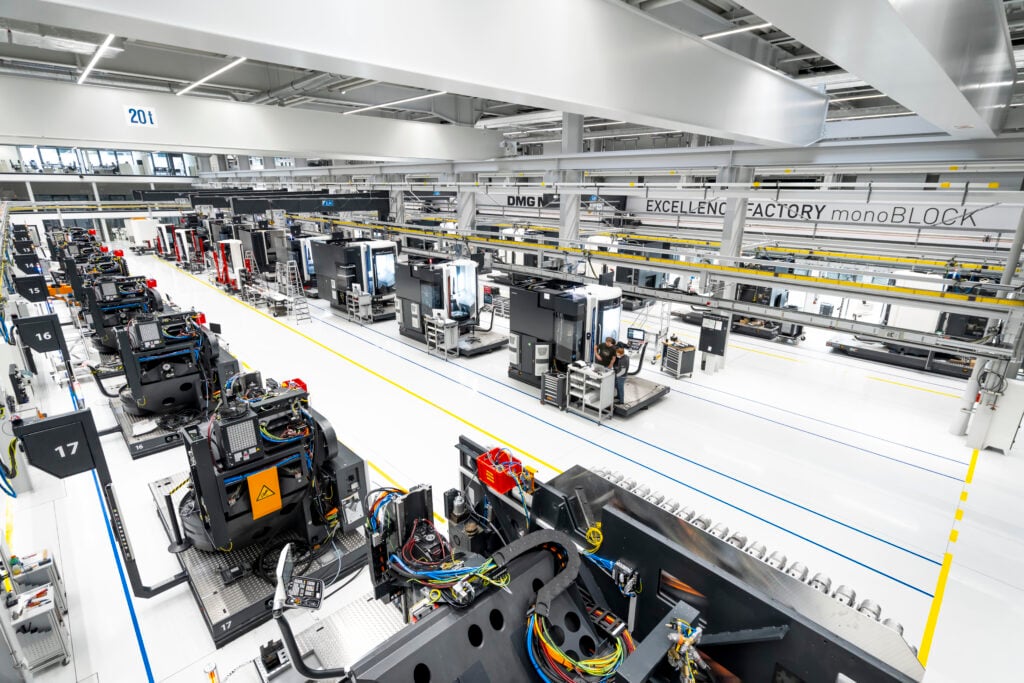
Functions
Each AGV has a capacity of 24 tonnes and a height of 400 mm. The AGVs move in two speed ranges: firstly, during assembly, they move continuously and fully automatically at a speed of 20-120 mm/min and secondly, during manual transportation, they can move at a speed up to 6000 mm/min to avoid congestion or slowing down due to other traffic in the area.
With their robust design, the low-built AGVs are perfect for continuous use in industrial environments. Each AGV is equipped with three wheels for optimum weight distribution, despite smaller floor inclines. The AGVs navigate using a QR code camera reading a QR code strip on the floor while the vehicle is travelling. This consists of simple adhesive strips on straight paths, while aluminum QR code strips are used in curves to withstand the bigger weight loads.
The AGVs communicate with the stationary control system via iWLAN for speed settings, emergency stops, status updates, etc. A graphic display shows the vehicles’ locations in the layout, while Solving’s stationary system continues to communicate with DMG MORI’s ERP system.
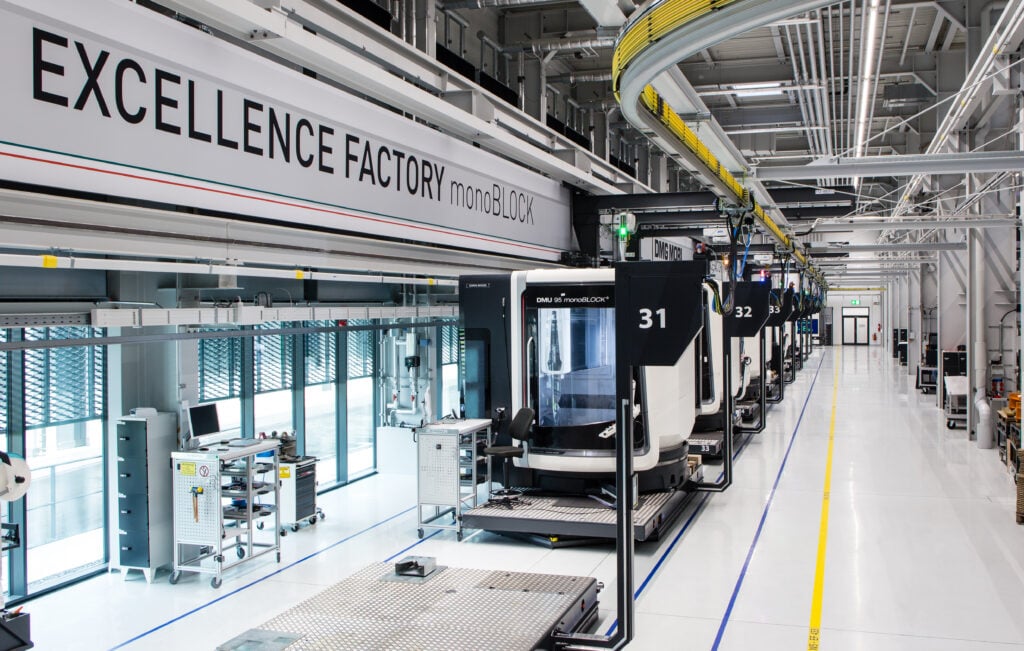
Safety: a central aspect
The safety precautions for the assembly platform are a key criterion. Safety is of utmost importance on and around the automated assembly platforms which are in continuous movement. This means that safety must be guaranteed in the environment, and while a crane is used during assembly and during assembly on the machine itself.
A SICK scanner programmed with different warning and safety areas ensures environmental safety. If an obstacle is detected on the route, the AGV stops automatically. If the laser scanners are blocked for too long, an acoustic and visual warning signal is activated. Additional safety bumpers on the AGVs increase safety and cause the device to stop immediately if touched.
The scanners also check the distances between the AGVs in the assembly line. As the components are lifted onto the platforms with cranes, a so-called soft stop is required during loading. For these situations, automatic catch-up reset the original distance between the AGVs.
Results and positive experiences
Markus Guggemoos, Process Manager monoBLOCK, at DMG MORI: “The system is characterized by high availability mainly due to solid technology. Another success factor is our early involvement in AGV technology. In case of challenges during operation, fast service was always available.”
The involvement of the employees in the project resulted in a high level of acceptance of the installation. The obvious advantages of the system, such as ergonomic platforms without stumbling hazards, were well accepted.
New installations planned
Tryggve Söderblom, Country Manager at Solving GmbH: “The excellent cooperation was characterized by a mutually constructive and challenging way of working, which led to further cooperation in several other DMG MORI plants.”